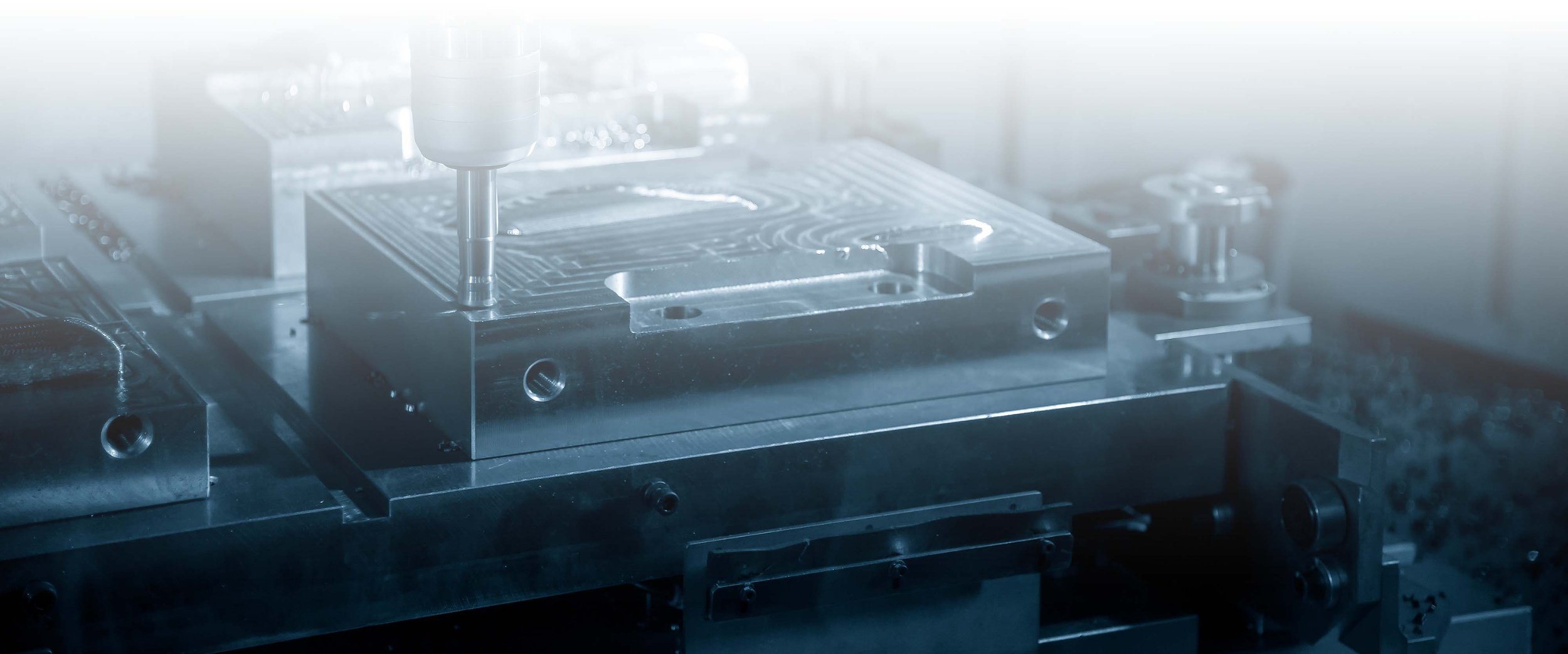
Design For Manufacturing Services
Utilizing cutting-edge CAD software, our team carefully considers each design choice throughout each phase of your project. By emphasizing manufacturability from the start, your product can come to life seamlessly.
Specialties
DFM For Injection Molded Parts
CNC Machining
3D Printing
Progressive Die Stamping
PCB & PCBA Development
Technical Drawing Generation
What Is Design For Manufacturing (DFM)
Design for manufacturing, often referred to as DFM, is the process of revising an existing design so that it can be manufactured using a specified technique. Common examples of these techniques include injection molding, sheet metal forming, CNC machining, and finishing. Each of these offers unique advantages and disadvantages in terms of material, startup costs, price per part, and mechanical constraints. All of which must be carefully considered to produce a product cost-effectively.
Deciding on which manufacturing process to use is a complex multi-layered question, which requires a copious amount of research and assumptions. In general, there are two primary considerations. The first is, what material would best suit the design’s form and function? The second is, what quantity you’re planning to produce the design. For example, CNC machining is a viable option for low quantity production due to the lack of tool costs. However, if you’re planning on higher quantities, then injection molding becomes more cost-effective despite the expensive tooling cost, as the price per piece is much lower.
When it comes to design for manufacturing, Kickstart Design is well versed in a wide range of manufacturing processes, the physical and material constraints required of a design, and the technical documentation needed to produce a cost-effective product. Our team is well versed in the DFM practices for manufacturing technologies, including, but not limited to:
Injection Molding
CNC Machining
3D Printing
Progressive Die Stamping
PCB & PCBA Development
Design For Injection Molding
One of the most common forms of mass production is injection molding. Primarily used in the production of plastic components, the injection molding process consists of heating plastic or rubber to a liquid state and then injecting it into a negative mold of the desired part. The main advantages of injection molding, and why it is so heavily used for mass production, is due to its high rate of production, and extremely low price per piece. The molded material is injected and cooled at such a rapid rate that a part can be completed in only a few seconds. This process is often entirely automated which contributes to the low price per piece.
However, injection molding also comes with a long list of disadvantages, the most notable of which is the immense cost and complexity of the mold itself. Most commonly machined from a block of solid steel, these precision tools can cost anywhere from thousands of dollars to hundreds of thousands. Additionally, parts produced via injection molding must be designed with unique considerations in mind. Considerations like overhang, draft, shrinkage, and many more.
Fortunately, the team at Kickstart Design shares a vast amount of knowledge and experience when it comes to designing parts for injection molding. Knowledge and experience that we use to reduce tooling costs and ensure a high-quality end product.